
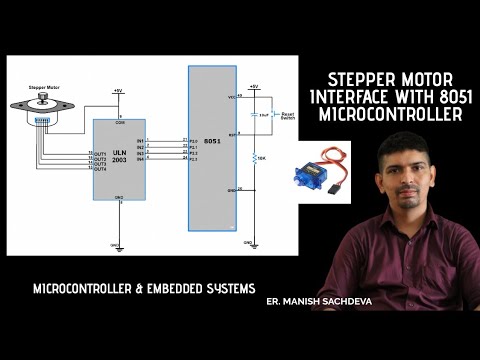
) The one in the ebay post moves 5.625° /64 (the motor itself move 5.625 degrees per step but the gear train divides that by 64.) With the gear train, I’m not sure how repeatable the steps are, so moving 10 steps right and then 10 steps left may not get you back to exactly the same place you started. In theory this project should be fairly easy, a stepper motor moves in fixed steps (hence the name. Probably not, Fritzing doesn’t currently have simulation so you need to use real hardware to test this. Once set up on Fritzing can I check somehow to see if it works, just on Fritzing or ? Once set up on Fritzing can I check somehow to see if it works, just on Fritzing or ? So I can then proceed to the physical Arduino etc. That will get me a long way and a lot more knowledgable. If the project url could show how to set up motor speed (always the same) set the stops, set the distance between stops. Will get more complicated than that (with reverse direction and selection of non sequential button) but at the moment just get it to go to next stop. At the moment just want to push button on and motor goes to next set stop. Four buttons on ‘in’ side to select the right stop. For a transfer table for a model railway, a small section of track moves sideways (driven by stepper motor) to each position. \$ P = VI = 24 \times 0.012 = 0.288\ \text W \$ so I would use a 0.5 W resistor for both the interface and additional load.Can someone help this aged challenged old man (77)Ĭan you give me a link to a stepper project that is for a stepper motor to have 4 steps (positions) to move a carriage between them. If you wanted you could add an LED in series with each resistor. That will draw an extra 12 mA and satisfy the output requirement without compromising the stepper input recommendation.

They would probably be fine at > 20 mA but without a datasheet for the opto-isolators it would be taking a chance.Ĭould a voltage divider placed between the driver and controller handle this problem? Maintain a voltage of 5 V at driver input pin and draw 21 mA current from the controller.Ī simpler solution would be to add a second 2k resistor to ground from each output. The stepper driver seems to be looking for about 10 mA per input for its opto-isolator LEDs.
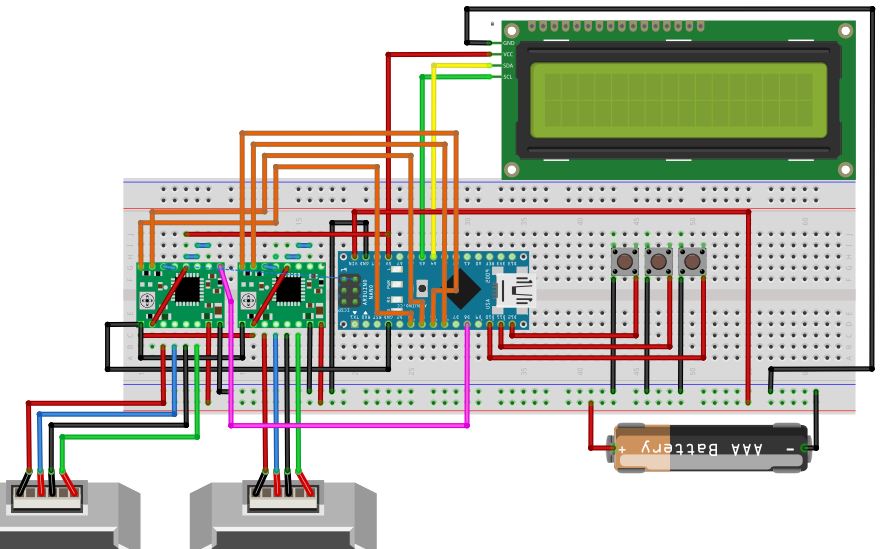
This will drop the current consumption below the 21 mA requirment of the controller.Ĭorrect. The ST-M5045 stepper driver data sheet says in order to use 24 volts as input a 2k resistor must be placed at the input. Since these are almost certainly opto-isolated FET outputs I would expect them to work down to a few volts but the table makes it look as though they are only rated for close to 24 V DC. and the output voltage of the pins are 24V. I have never seen a minimum current specification like that before. There is a minimum current requirement in order to use the FET pins on the Micrologix controller of 21 mA.
